Tarrina Miller is currently working as a consultant for EPS. With more than 20 years of experience of delivering change in a variety of manufacturing settings, she is helping us to look afresh about the way we do things as a business.
With defence capabilities firmly back on the agenda and governments across Europe dialling up the proportion of GDP they spend, the need to be lean and efficient across all levels of the business and stages of production has never been more important.
As a LEAN and best practice coach Tarrina works with businesses to help them on their improvement journeys and we’ve been delighted to have her on board to identify changes to the way we operate that will benefit the business for the long term.
We caught up with Tarrina on-site to talk about the project to date, the best practices already in place and changes to come that will put EPS in a great position to further drive efficiencies and increase capacity to meet future demand.
What was your brief for this project with EPS?
EPS wanted to introduce some fresh modern thinking to their on-site operations including best practice, tools and techniques that could benefit production and the wider business.
What was the starting point?
I visited the site back last August and did four days of scoping, talking to the workshop staff in each of the departments and then feeding back with some suggested areas of opportunity to do things differently.
That scoping involved seeing the layout of the workspace, including how the lines were organised, the flow of materials and how bespoke the manufacturing operations were.
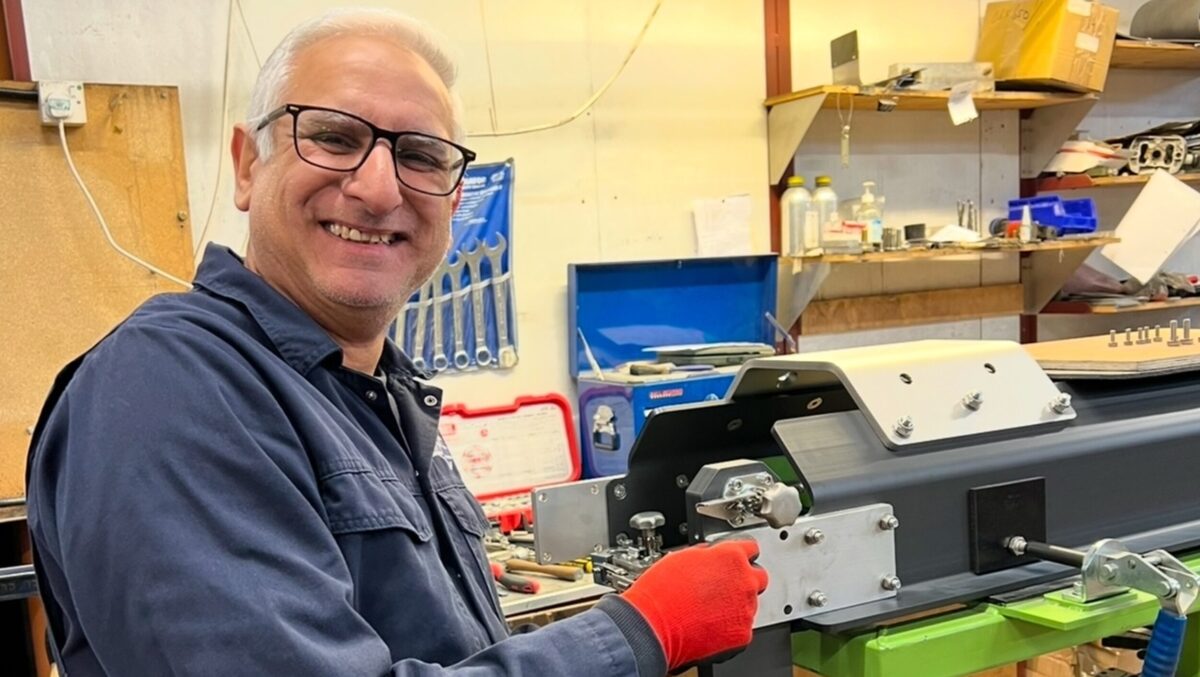
What impressed you about the EPS manufacturing process?
The quality of the product leaving the workshop is exceptional. What really struck me at the start was the sheer attention to detail on meeting the customer specification.
When you see the final article leaving the site, it’s brilliantly done and a real testament to the skills and craftmanship of the workforce
What can the challenges be for projects like this?
I’ve gone into lots of businesses where it’s very easy for people to get used to where they’re at and how things currently are.
Whereas being an independent consultant and coming in with a view on how things could look I can walk around and see what needs to move, what needs to come out, the flow is coming through here well, but we’ve got a bottleneck there. Part of what I’ve been trying to do is to work with staff to say: ‘Let’s look at this with fresh eyes.’
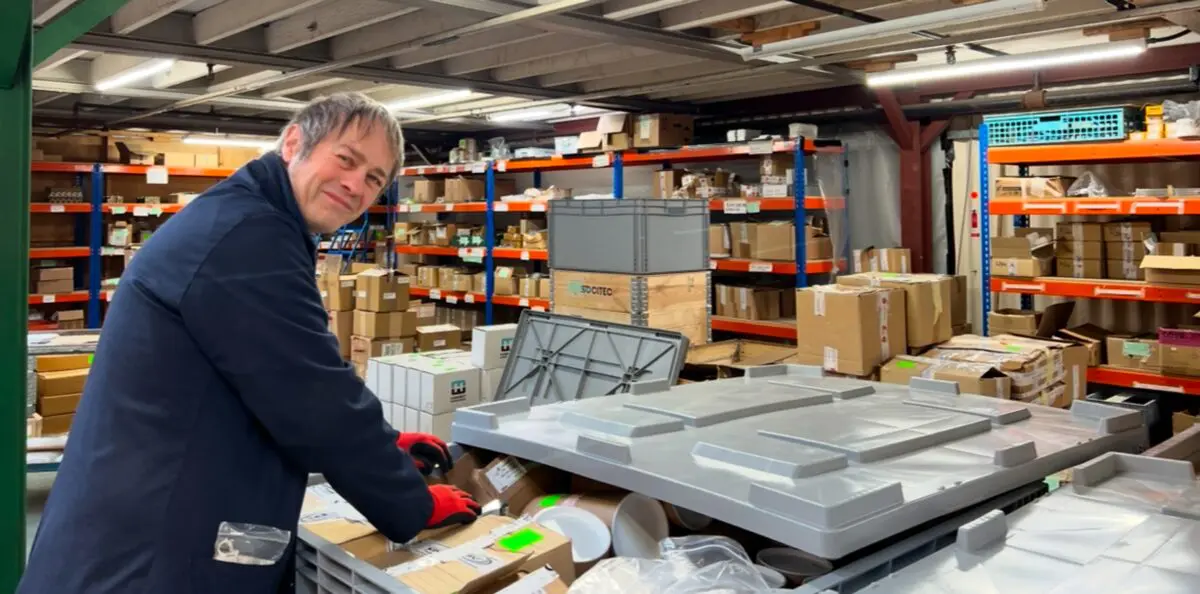
What were those areas of opportunities that were identified?
The initial thoughts were around pushing the 5S model around workplace organisation. It’s the foundation stone for lean manufacturing: having everything in its right place and removing anything that’s no longer needed.
This is an iterative process and, given the size of the space, is likely to continue across the rest of 2025. Our focus has been on the workshop space: from stores through to each of the project streams and product lines that are running.
My view was that the product leaving the workshop was exceptional, yet the surrounding environment didn’t match up and could be made to look and work better. My role is to help the team go to the next level by improving the space in which they work and the processes they follow.
Take us through the 5S model what it seeks to achieve
The 5S’s represent five stages of workplace organisation:
SORT – Getting what you don’t need out of the production area.
STRAIGHTEN – Identify what you need in the area and where best to locate it.SHINE – Deep clean of the work area and visual improvements including signage.
STANDARDISING – Set ground rules for maintaining the area with operators and workshop staff
SUSTAIN – Internal auditing to make sure the improvements are maintained.
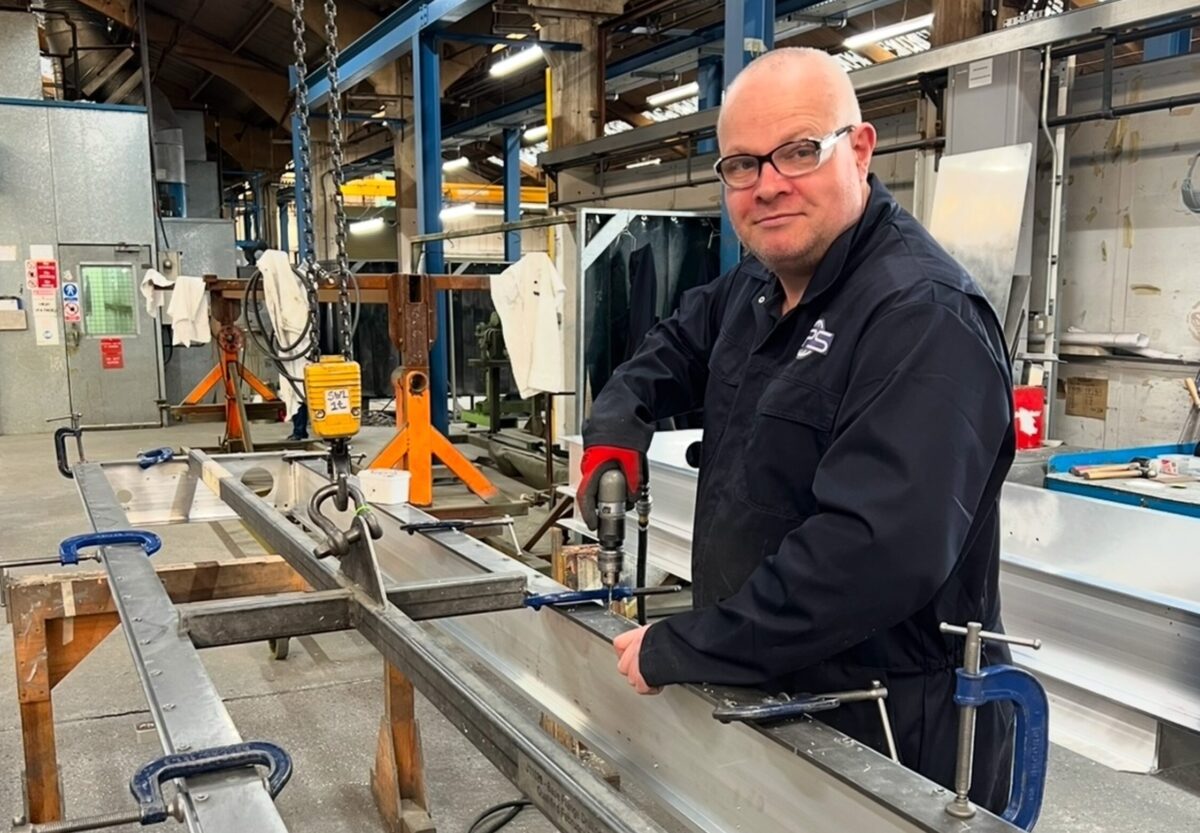
Has this been a collaborative exercise?
We’ve done a lot of engagement sessions around what 5S is, what continuous improvement is all about and why it may be beneficial to look at things with fresh eyes.
It’s not been a case of turning up and forcing change but rather explaining the benefits and then working with the team to try things, to pilot and see the results.
Feedback from staff has been important in flagging areas for improvement, including things like putting up tier boards for different levels of meetings. We’ve been able to draft up concept ideas ready to pilot , refine and then go with final implementation. It’s all done very much in a collaborative way.
What’s been the response so far to work you’ve done?
Everyone I’ve spoken to has been engaged. People can see there is a real opportunity to lift and transform the appearance and flow of the space so it’s much brighter, cleaner and well set out. As a result, production flow will improve.
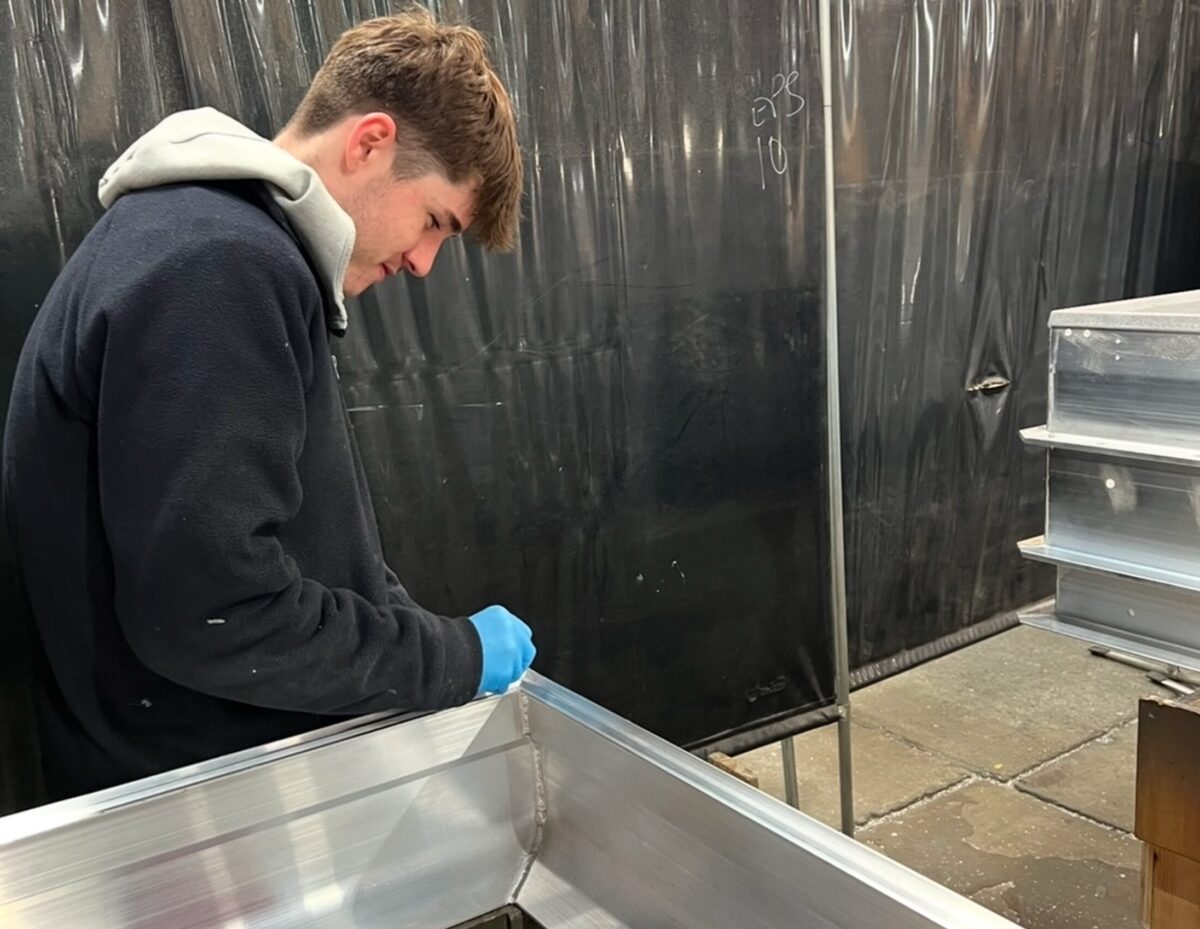
What other elements of the LEAN process are you looking to deliver?
The LEAN process includes identifying and eliminating what are known as the eight wastes. This includes things like double handling and the amount of footwork or steps people need to do per day. Any lost time looking for things will be eliminated.
What we’re trying to do is to drive efficiency and minimise the potential for damage, for example, if you’re having to constantly move your product from A to B. If you can flow it without having to move it so often, you can get a quality improvement as well. It’s about creating more time, more focus, and more productivity through the lines.
We’ll be starting a second phase mid-year looking at timings allocated to tasks. This isn’t about time-in-motion but more a case of identifying what could be done to speed up the process. That could be a simple improvement in tooling or a jig. We’ll be working bite-sized along each of the production lines and really looking at whether the process is as tight as it can be.
The idea is to crush out any kind of non-value-added steps that could be holding things up. We will also look at useful performance indicators (KPIs) and metrics that will allow performance feedback and flag where further improvement may be required.